Setting the correct temperature on your water heater is essential for both safety and energy efficiency. If the temperature is too high, you risk burns and scalds, while a temperature that’s too low could promote bacteria growth and leave you with lukewarm water. So, what temperature should a hot water heater be set at? Let’s explore the ideal temperature settings for your home.
What Temperature Should Water Heater Be Set At for Safety?
According to the U.S. Department of Energy, the optimal temperature setting for most households is 120°F (49°C). At this temperature, you minimize the risk of scalding while ensuring that the water is hot enough to kill harmful bacteria like Legionella, which can grow in lukewarm water. Many homeowners wonder, “what temp should water heater be set at” to strike a balance between safety and comfort. A setting of 120°F is generally recommended to protect your family, especially if you have young children or elderly individuals who are more susceptible to burns.
What Temperature Should the Water Heater Be Set At for Efficiency?
In addition to safety, what temperature should the water heater be set at for optimal energy efficiency? A setting of 120°F (49°C) is again ideal because it minimizes energy consumption without sacrificing comfort. Water heaters account for a significant portion of a home’s energy use, and for every 10°F reduction in temperature, you can save between 3% and 5% on energy costs.

If you’ve been wondering what should water heater temperature be set at to keep your energy bills in check, 120°F offers the best balance. Setting it higher may waste energy, while a lower temperature might not provide the comfort you expect.
Factors That May Affect Water Heater Temperature Settings
While 120°F is the standard recommendation, some factors may influence whether you need to adjust this setting:
- Household Size: Larger households may require a higher temperature to meet the hot water demands of multiple users. However, if you choose to increase the temperature, be cautious to avoid scalding risks.
- Dishwashers Without Built-In Heaters: If your dishwasher does not have its own heating element, you may need to set the water heater at 140°F (60°C) for effective cleaning.
- Compromised Immune Systems: For households with members who have weakened immune systems, a higher water temperature (around 140°F) may be necessary to kill bacteria effectively.
Understanding these factors can help you answer the question, “at what temperature should a water heater be set” in your specific situation.
Why Not Set the Temperature Higher?
You might be tempted to set your water heater to a higher temperature, thinking it will deliver hotter water faster. However, setting your heater above 120°F increases the risk of severe burns. According to the American Burn Association, water at 140°F can cause third-degree burns in just five seconds, which is why it’s important to consider what should the temperature be on a hot water heater to maintain safety in your home.
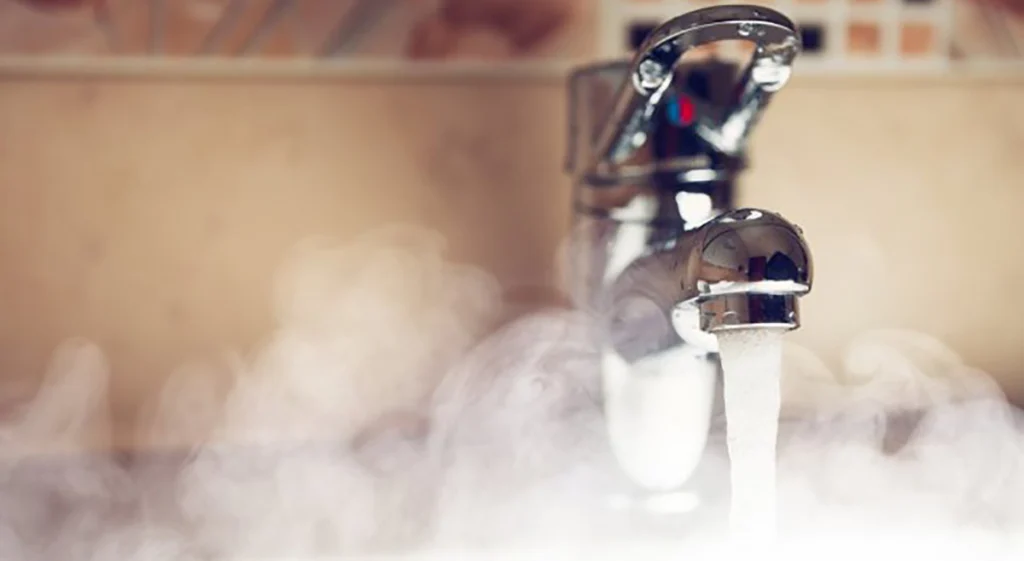
What Temperature Should I Set My Hot Water Heater To in Cold Climates?
In colder climates, homeowners often wonder what temperature should I set my hot water heater to when the weather drops. While it may seem logical to increase the water heater’s temperature during colder months, 120°F should still be sufficient. However, if you notice that the water cools too quickly or isn’t reaching the expected temperature, you may need to check the insulation on your pipes or heater, rather than increasing the temperature setting.
How to Adjust Your Water Heater Temperature
If you’ve decided to adjust your water heater, here are the steps to follow:
- Turn Off the Power: If you have an electric heater, switch off the power at the breaker. For gas heaters, set the gas control to “pilot.”
- Locate the Temperature Dial: Most water heaters have a thermostat dial located near the bottom of the unit.
- Adjust the Temperature: Turn the dial to the desired temperature (120°F or 140°F, depending on your needs). Use a thermometer to verify the actual temperature after the adjustment.
- Wait and Test: After making adjustments, allow the water to heat for a few hours, then test the temperature at various faucets to ensure accuracy.
By following these steps, you can easily control what temp should water heater be for your home’s safety and efficiency.
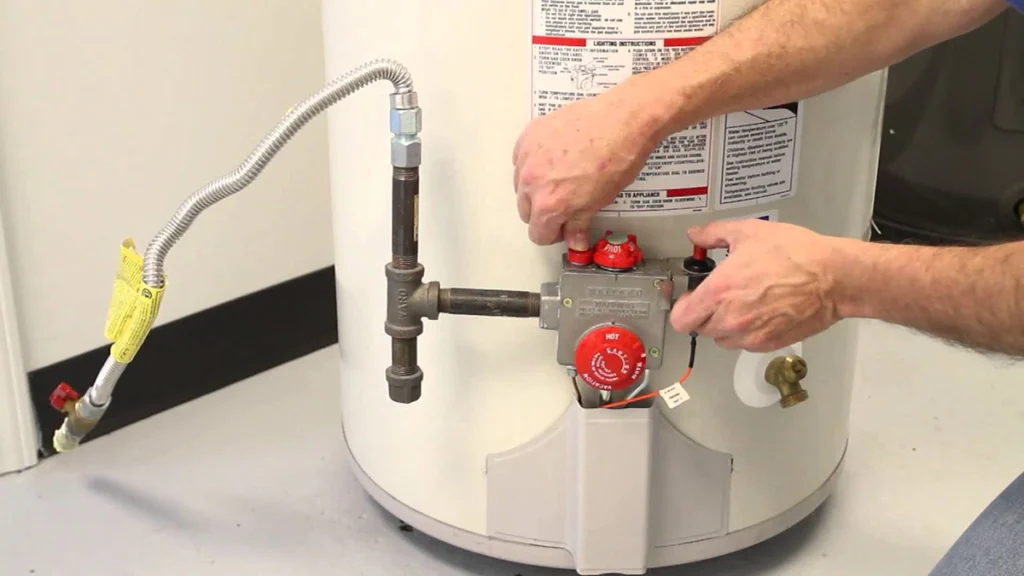
Conclusion
When considering what temperature should water heater be set at, the safest and most efficient option for most homes is 120°F. This temperature reduces the risk of scalding, conserves energy, and is hot enough to kill bacteria. In some cases, you may need to adjust the temperature to 140°F for specific appliances or health concerns. By understanding what temp should water heater be set at for your household’s needs, you can maintain a safe, energy-efficient, and comfortable living environment.