Maintaining process piping is crucial for ensuring the safety, efficiency, and longevity of industrial operations. Whether you’re in the oil and gas sector, chemical processing, or any other industry relying on process piping, these systems are the lifeblood of your operations. In this article, we’ll delve into five essential tips to keep your process piping in top-notch condition, ensuring your operations run smoothly and safely.
Contents
- 1 Regular Inspections
- 2 Proper Cleaning
- 2.1 Regular Cleaning Schedule
- 2.2 Cleaning Methods
- 2.3 Preventative Measures
- 2.4 Corrosion Control
- 2.5 Monitoring and Maintenance
- 2.6 Safety Considerations
- 2.7 Monitoring and Control
- 2.8 Real-Time Monitoring
- 2.9 Automated Control Systems
- 2.10 Alarm and Alert Systems
- 2.11 Predictive Maintenance
- 2.12 System Optimization
- 2.13 Documentation and Reporting
- 2.14 Safety Considerations
- 3 Corrosion Prevention
- 4 Scheduled Maintenance and Repairs
- 4.1 Develop a Maintenance Schedule
- 4.2 Routine Inspections
- 4.3 Preventative Maintenance Tasks
- 4.4 Address Minor Repairs Promptly
- 4.5 Schedule Major Repairs
- 4.6 Documentation and Record-Keeping
- 4.7 Staff Training and Safety
- 4.8 Monitoring and Feedback
- 4.9 Budgeting and Resource Allocation
- 4.10 Collaboration and Communication
- 4.11 FAQs
Regular Inspections
Regular inspections are a cornerstone of effective process piping maintenance. These inspections help identify potential issues before they become major problems, ensuring the system operates smoothly and efficiently. Here are some key points to consider when conducting regular inspections:
Visual Inspections
- Frequency: Conduct visual inspections regularly, such as weekly or monthly, depending on the criticality and usage of the piping system.
- Focus Areas: Look for visible signs of wear and tear, such as rust, corrosion, leaks, cracks, and loose fittings.
- Documentation: Keep detailed records of each inspection, noting any anomalies or areas that need attention. This documentation helps track the system’s condition over time.
Advanced Inspection Techniques
- Ultrasonic Testing: Use ultrasonic testing to measure the thickness of the pipe walls and detect internal corrosion or erosion. This non-destructive method is highly effective for identifying hidden issues.
- Radiography: Employ radiographic testing to get detailed images of the internal structure of pipes. This technique can reveal cracks, weld defects, and other hidden damages.
- Magnetic Particle Testing: This method is useful for detecting surface and slightly subsurface cracks in ferromagnetic materials. It involves applying a magnetic field and then using magnetic particles to identify discontinuities.
Leak Detection
- Acoustic Monitoring: Implement acoustic monitoring devices to detect leaks by listening for the sound of escaping fluid. This method is particularly useful for high-pressure systems.
- Pressure Testing: Periodically conduct pressure tests to ensure the system can withstand its operational pressures. Monitor for any drops in pressure that might indicate a leak.
Corrosion Monitoring
- Corrosion Coupons: Place corrosion coupons within the piping system to measure the rate of corrosion over time. These are small metal samples that corrode at the same rate as the pipes, providing valuable data on the corrosiveness of the environment.
- Electrochemical Techniques: Use electrochemical monitoring methods, such as linear polarization resistance (LPR), to measure corrosion rates in real-time.
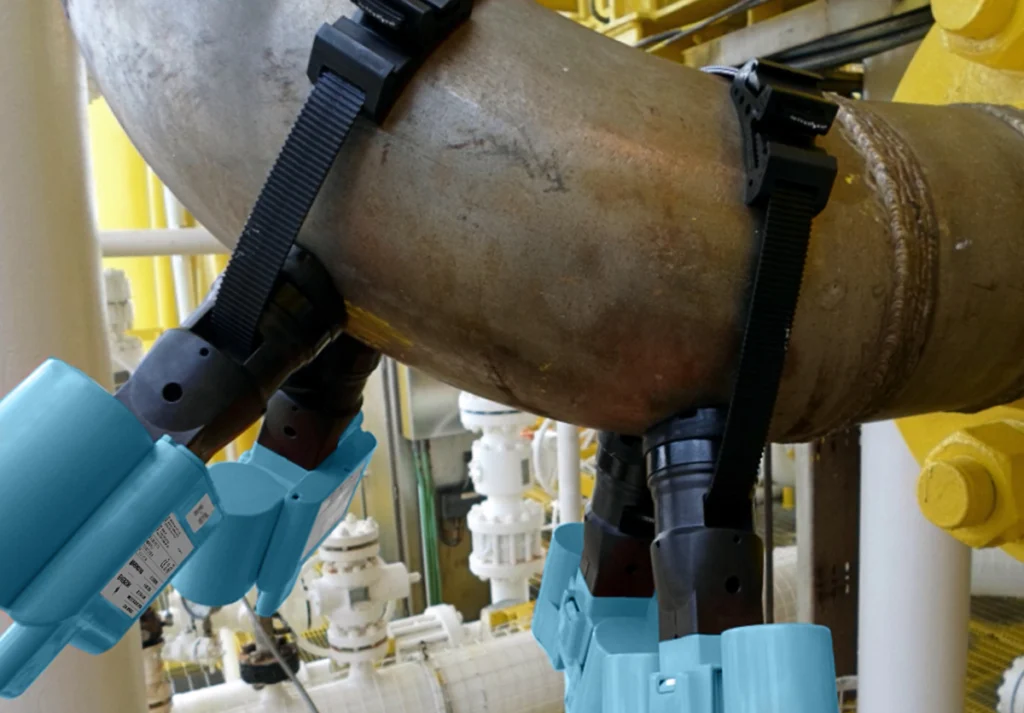
Safety Considerations
- Personal Protective Equipment (PPE): Always wear appropriate PPE during inspections to protect against potential hazards.
- System Shutdowns: For more intrusive inspections, such as internal pipe examinations, plan for system shutdowns to ensure safety and minimize disruption.
Reporting and Follow-up
- Immediate Reporting: Report any critical findings immediately to the maintenance team or management to initiate prompt repairs.
- Follow-up Actions: Schedule follow-up inspections or maintenance activities based on the findings. Prioritize areas that show signs of significant wear or potential failure.
Regular inspections not only help maintain the integrity and performance of the piping system but also contribute to overall safety and reliability. By catching issues early, you can avoid costly repairs and unplanned downtime, ensuring smooth and efficient operations.
Proper Cleaning
Proper cleaning of process piping systems is essential to maintain optimal performance and prevent issues such as blockages, corrosion, and contamination. Here are key strategies for ensuring your piping system remains clean and efficient:
Regular Cleaning Schedule
- Frequency: Establish a cleaning schedule based on the type of materials transported through the pipes and the operational environment. High-use systems or those transporting potentially corrosive or clogging substances may require more frequent cleaning.
- Documentation: Keep detailed records of cleaning activities, including dates, methods used, and any observations. This helps track the effectiveness of the cleaning process and plan future maintenance.
Cleaning Methods
- Mechanical Cleaning (Pigging):
- Description: Pigging involves sending a device known as a “pig” through the pipes to scrape and push out debris and buildup.
- Application: Effective for removing solid deposits, scale, and soft blockages. Suitable for long pipelines and systems with few bends.
- Types of Pigs: Different pigs (e.g., foam, scraper, brush) are used depending on the nature of the deposits and the pipe material.
- Chemical Cleaning:
- Description: Chemical cleaning uses specific solutions to dissolve and remove deposits, such as scale, rust, and biofilms.
- Application: Useful for removing mineral scales, organic buildup, and corrosion products. Ensure the chosen chemicals are compatible with the pipe material.
- Safety Precautions: Handle chemicals with care, using appropriate personal protective equipment (PPE) and following safety guidelines to prevent chemical exposure or damage to the system.

- Hydro Jetting:
- Description: Hydro jetting involves using high-pressure water jets to clean the inside of pipes.
- Application: Highly effective for removing stubborn clogs, grease, and mineral deposits. Suitable for a wide range of pipe materials and diameters.
- Equipment: Requires specialized equipment and trained personnel to operate safely and effectively.
Preventative Measures
- Filtration Systems: Install filtration systems to remove particles and contaminants before they enter the piping system. This reduces the frequency of cleaning needed and helps maintain system integrity.
- Regular Flushing: Periodically flush the system with water or other compatible fluids to remove loose debris and prevent buildup. This is particularly important in systems where sediment accumulation is common.
Corrosion Control
- Corrosion Inhibitors: Use corrosion inhibitors in cleaning solutions to protect pipe surfaces from corrosion during and after the cleaning process.
- Material Selection: Choose corrosion-resistant materials for pipes and fittings to minimize the impact of cleaning chemicals and extend the lifespan of the system.
Monitoring and Maintenance
- Inspection After Cleaning: Inspect the piping system after each cleaning to ensure all deposits and contaminants have been effectively removed. Use visual inspections and advanced techniques like borescopes or endoscopes.
- Routine Maintenance: Combine regular cleaning with other maintenance activities, such as inspecting for leaks, checking pressure and flow rates, and replacing worn components.

Safety Considerations
- Personal Protective Equipment (PPE): Ensure all personnel involved in cleaning operations wear appropriate PPE, such as gloves, goggles, and protective clothing.
- Ventilation: Provide adequate ventilation when using chemical cleaners to prevent the buildup of harmful fumes.
- Training: Ensure that all personnel involved in cleaning operations are properly trained in the safe handling and application of cleaning methods and chemicals.
Proper cleaning of your process piping system is essential to maintaining its efficiency, preventing downtime, and extending its lifespan. By following these guidelines, you can ensure that your system remains in optimal condition and continues to operate smoothly.
Monitoring and Control
Monitoring and control are critical components of effective process piping maintenance. By keeping a close watch on your piping system’s performance and implementing automated control mechanisms, you can detect issues early, optimize operations, and prevent costly downtime. Here are key strategies for monitoring and controlling your process piping system:
Real-Time Monitoring
- Sensors and Instrumentation: Install sensors throughout the piping system to continuously monitor key parameters such as pressure, temperature, flow rate, and fluid levels. Common sensors include pressure transducers, temperature sensors, flow meters, and level sensors.
- Data Collection: Use data loggers and acquisition systems to collect and store data from sensors. This data provides valuable insights into the system’s performance over time and helps identify trends and anomalies.
Automated Control Systems
- Programmable Logic Controllers (PLCs): Implement PLCs to automate the control of various processes within the piping system. PLCs can be programmed to respond to sensor data, adjusting valves, pumps, and other components to maintain optimal operating conditions.
- Supervisory Control and Data Acquisition (SCADA): Utilize SCADA systems for centralized monitoring and control. SCADA systems integrate data from multiple sensors and PLCs, providing a comprehensive view of the entire piping network. Operators can use SCADA interfaces to make real-time adjustments and respond to alarms.
Alarm and Alert Systems
- Threshold Settings: Set thresholds for critical parameters such as pressure and temperature. When these thresholds are exceeded, the system should trigger alarms or alerts to notify operators of potential issues.
- Automated Responses: Configure automated responses for certain alarms. For example, if a pressure sensor detects a dangerous increase in pressure, the system can automatically shut down the affected section of the piping to prevent damage.
Predictive Maintenance
- Condition Monitoring: Use condition monitoring techniques to predict potential failures before they occur. This can include vibration analysis, thermal imaging, and acoustic monitoring. By understanding the normal operating conditions, deviations can indicate the need for maintenance.
- Predictive Analytics: Employ predictive analytics tools to analyze historical data and predict future performance. Machine learning algorithms can identify patterns and forecast potential failures, allowing for proactive maintenance planning.
System Optimization
- Flow Rate Control: Monitor and adjust flow rates to ensure efficient operation. Use variable frequency drives (VFDs) on pumps and motors to optimize energy usage and reduce wear and tear on equipment.
- Pressure Management: Implement pressure control systems to maintain consistent pressure levels throughout the piping network. This helps prevent stress on pipes and fittings, reducing the risk of leaks and bursts.
Documentation and Reporting
- Data Logging: Maintain detailed logs of all monitoring data, control actions, and maintenance activities. This documentation helps track system performance, identify recurring issues, and improve future maintenance strategies.
- Reporting: Generate regular reports summarizing the system’s performance, including any incidents, maintenance actions, and recommendations for improvements. These reports provide valuable insights for management and help ensure accountability.
Safety Considerations
- Emergency Shutdown Systems: Ensure that emergency shutdown systems are in place and regularly tested. These systems should be able to quickly isolate sections of the piping network in case of a critical failure.
- Training: Provide ongoing training for operators and maintenance personnel on the use of monitoring and control systems. Ensure they are familiar with the procedures for responding to alarms and performing corrective actions.
By implementing effective monitoring and control strategies, you can enhance the reliability, efficiency, and safety of your process piping system. This proactive approach helps identify and address issues before they escalate, ensuring smooth and continuous operation.
Corrosion Prevention
Corrosion is a major concern for process piping systems, as it can lead to leaks, system failures, and costly repairs. Implementing effective corrosion prevention strategies is essential to extend the lifespan of your piping and ensure reliable operation. Here are key methods for preventing corrosion in process piping systems:
Protective Coatings
- Epoxy Coatings: Apply epoxy coatings to the interior and exterior surfaces of pipes. These coatings provide a barrier that prevents corrosive substances from coming into direct contact with the pipe material.
- Polyurethane Coatings: Use polyurethane coatings for their excellent resistance to abrasion and chemical attack. They are suitable for both metal and concrete surfaces.
- Galvanizing: For steel pipes, consider galvanizing, which involves applying a protective layer of zinc to prevent rust and corrosion.
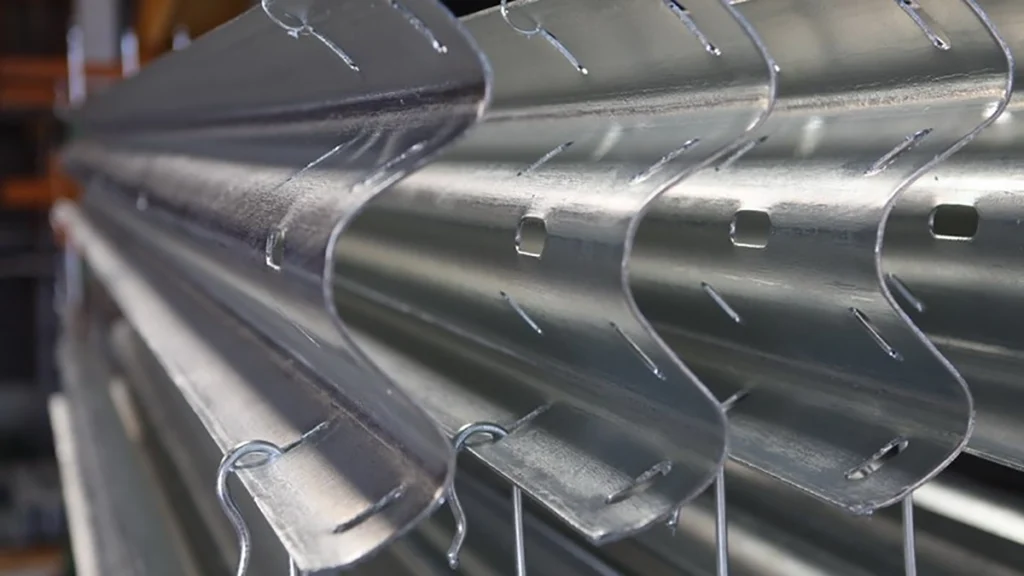
Cathodic Protection
- Sacrificial Anodes: Install sacrificial anodes, such as magnesium or zinc rods, which corrode in place of the piping material. This method is effective for buried or submerged pipes.
- Impressed Current Systems: Use impressed current systems to provide a continuous electrical current that counteracts the corrosive electrochemical process. This method is suitable for large piping networks and offers long-term protection.
Corrosion Inhibitors
- Chemical Inhibitors: Add corrosion inhibitors to the fluid transported through the pipes. These chemicals form a protective film on the pipe’s surface, reducing the rate of corrosion.
- Types of Inhibitors: Use different types of inhibitors based on the nature of the fluid and the material of the pipes, such as anodic inhibitors, cathodic inhibitors, and mixed inhibitors.
Material Selection
- Corrosion-Resistant Materials: Choose materials that are naturally resistant to corrosion for your piping system. Common options include stainless steel, copper, and plastic polymers like PVC and CPVC.
- Alloyed Metals: Use alloyed metals, such as chromium or nickel alloys, which offer enhanced corrosion resistance compared to pure metals.
Environmental Control
- Humidity Control: Reduce humidity levels in areas where pipes are exposed to moisture. Use dehumidifiers and proper ventilation to keep the environment dry.
- Temperature Control: Maintain stable temperatures to prevent thermal cycling, which can accelerate corrosion. Use insulation to protect pipes from extreme temperature fluctuations.
Regular Maintenance and Monitoring
- Inspection and Testing: Conduct regular inspections and non-destructive testing to detect early signs of corrosion. Techniques such as ultrasonic testing, radiography, and visual inspections are effective for monitoring the condition of pipes.
- Maintenance Schedule: Implement a proactive maintenance schedule that includes cleaning, re-coating, and replacing corroded sections of piping as needed.
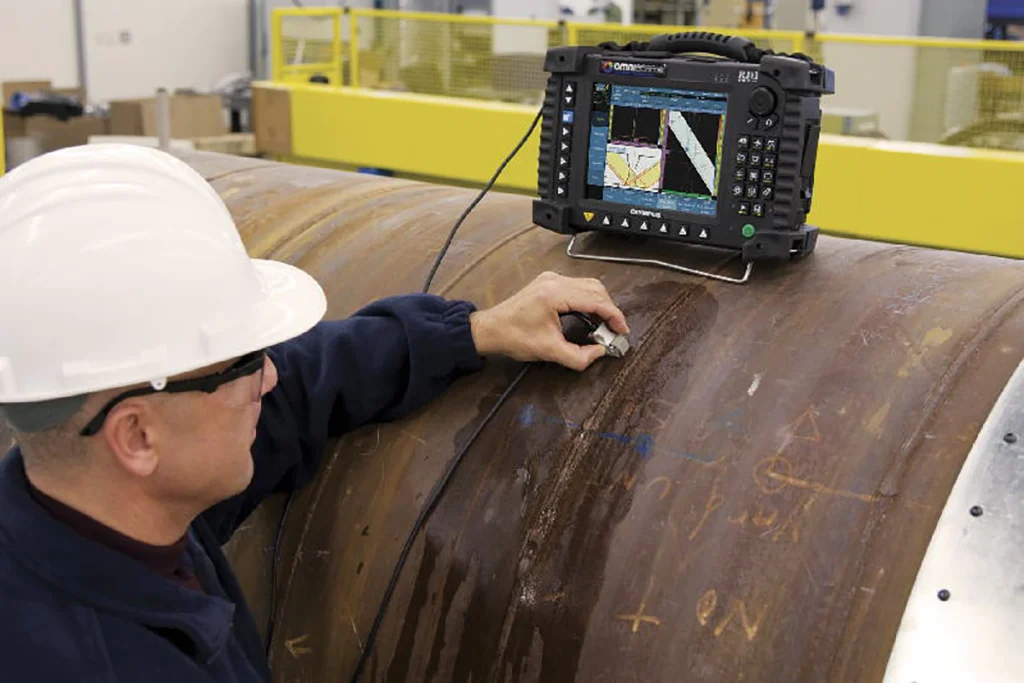
Design Considerations
- Proper Drainage: Design piping systems with proper drainage to prevent water accumulation, which can accelerate corrosion. Ensure there are adequate slopes and drains.
- Avoiding Trapped Air: Design the system to minimize trapped air pockets, which can create oxygen-rich environments that promote corrosion.
Quality Control
- Material Quality: Ensure that all materials used in the piping system meet industry standards for quality and corrosion resistance.
- Installation Practices: Follow best practices for installation, including proper welding techniques, joint sealing, and ensuring that protective coatings are not damaged during installation.
Environmental and Chemical Controls
- Neutralizing Agents: Use neutralizing agents to balance the pH levels of fluids flowing through the pipes, reducing the risk of acidic or alkaline corrosion.
- Contaminant Removal: Filter out contaminants from the fluid that could contribute to corrosion, such as oxygen, chlorine, and sulfur compounds.
By implementing these corrosion prevention strategies, you can protect your process piping system from degradation, ensuring long-term reliability and reducing maintenance costs. Regular monitoring and proactive maintenance are key to effectively managing corrosion and extending the lifespan of your piping infrastructure.
Scheduled Maintenance and Repairs
Scheduled maintenance and repairs are essential for ensuring the longevity and reliability of process piping systems. By proactively addressing potential issues and performing regular upkeep, you can prevent unexpected failures, reduce downtime, and maintain optimal performance. Here are key strategies for effective scheduled maintenance and repairs:

Develop a Maintenance Schedule
- Regular Intervals: Establish a maintenance schedule with regular intervals based on the type of system, usage, and environmental conditions. Common intervals include weekly, monthly, quarterly, and annually.
- Customized Plans: Tailor the maintenance schedule to the specific needs of your piping system. Consider factors such as the age of the system, material, and any known vulnerabilities.
Routine Inspections
- Visual Inspections: Conduct routine visual inspections to identify signs of wear, corrosion, leaks, and other potential issues. These inspections should be part of the regular maintenance schedule.
- Advanced Inspections: Utilize advanced inspection techniques such as ultrasonic testing, radiographic testing, and thermal imaging to detect hidden issues that may not be visible during a visual inspection.
Preventative Maintenance Tasks
- Cleaning: Regularly clean the piping system to remove debris, scale, and other buildup that can lead to clogs and corrosion. Use methods such as pigging, chemical cleaning, and hydro jetting.
- Lubrication: Apply appropriate lubricants to moving parts, such as valves and pumps, to reduce friction and wear.
- Re-Coating: Reapply protective coatings to pipes as needed to prevent corrosion and other forms of degradation.
Address Minor Repairs Promptly
- Leak Repair: Fix minor leaks as soon as they are detected to prevent them from becoming major issues. Use appropriate sealants, clamps, or replacement parts.
- Pipe Replacement: Replace sections of pipe that show significant wear, corrosion, or damage. This can prevent more extensive repairs in the future.
Schedule Major Repairs
- Planned Shutdowns: Plan for major repairs during scheduled shutdowns to minimize disruption to operations. Coordinate with relevant departments to ensure that the shutdown is as short and efficient as possible.
- Replacement Projects: Schedule the replacement of major components, such as valves, pumps, and large sections of piping, based on their expected lifespan and condition.
Documentation and Record-Keeping
- Maintenance Logs: Keep detailed records of all maintenance activities, including inspections, cleaning, repairs, and replacements. Document the date, personnel involved, and any observations or findings.
- Historical Data: Use historical maintenance data to identify patterns and predict future maintenance needs. This can help in planning and budgeting for upcoming maintenance activities.
Staff Training and Safety
- Training Programs: Provide ongoing training for maintenance staff to ensure they are knowledgeable about the latest techniques, tools, and safety procedures. Well-trained staff are essential for effective maintenance and repair.
- Safety Protocols: Implement and enforce strict safety protocols to protect maintenance personnel. Ensure that all staff are equipped with appropriate personal protective equipment (PPE) and are aware of potential hazards.
Monitoring and Feedback
- Performance Monitoring: Continuously monitor the performance of the piping system using sensors and data analysis. This can help detect issues early and provide feedback on the effectiveness of maintenance activities.
- Regular Reviews: Conduct regular reviews of the maintenance program to identify areas for improvement. Use feedback from maintenance staff and system performance data to make adjustments to the schedule and procedures.
Budgeting and Resource Allocation
- Budget Planning: Allocate sufficient budget for regular maintenance and unexpected repairs. This ensures that financial constraints do not hinder essential maintenance activities.
- Resource Management: Ensure that necessary tools, equipment, and replacement parts are readily available. Proper resource management can reduce downtime and improve the efficiency of maintenance operations.
Collaboration and Communication
- Interdepartmental Coordination: Foster collaboration and communication between maintenance teams and other departments, such as operations and engineering. This ensures that everyone is aware of scheduled maintenance activities and can plan accordingly.
- Stakeholder Involvement: Involve key stakeholders in the planning and review of the maintenance program. Their input can provide valuable insights and support for maintenance initiatives.
By implementing a comprehensive scheduled maintenance and repair program, you can ensure the reliability and efficiency of your process piping system. Proactive maintenance helps prevent unexpected failures, reduces downtime, and extends the lifespan of your infrastructure, ultimately saving time and money.
FAQs
Regular inspections are crucial because they help identify potential issues early, such as leaks, corrosion, and wear and tear. Early detection allows for timely repairs, preventing minor issues from becoming major problems that could lead to system failures or costly downtime.
A regular inspection should include visual checks for signs of damage, leaks, and corrosion. Advanced techniques like ultrasonic testing and radiographic inspections can detect hidden issues. It’s also important to monitor for unusual noises or vibrations that might indicate problems.
The frequency of cleaning depends on the type of materials being transported and the operational environment. Generally, pipes should be cleaned at regular intervals, such as quarterly or annually. High-use systems or those handling corrosive or clogging substances may require more frequent cleaning.
Effective methods for cleaning process piping include pigging (mechanical cleaning), chemical cleaning, and hydro jetting. The choice of method depends on the type of deposits and the material of the pipes. Each method has its own advantages and is suited for different cleaning needs.
Performance can be monitored using sensors to track key parameters such as pressure, temperature, and flow rates. Implementing data loggers and SCADA systems allows for real-time monitoring and automated control. Regular data analysis helps detect anomalies and optimize system performance.